Reverse Logistics 101:
Everything you need to know
Learn all there is to know about Reverse Logistics and how to optimize your return processes.
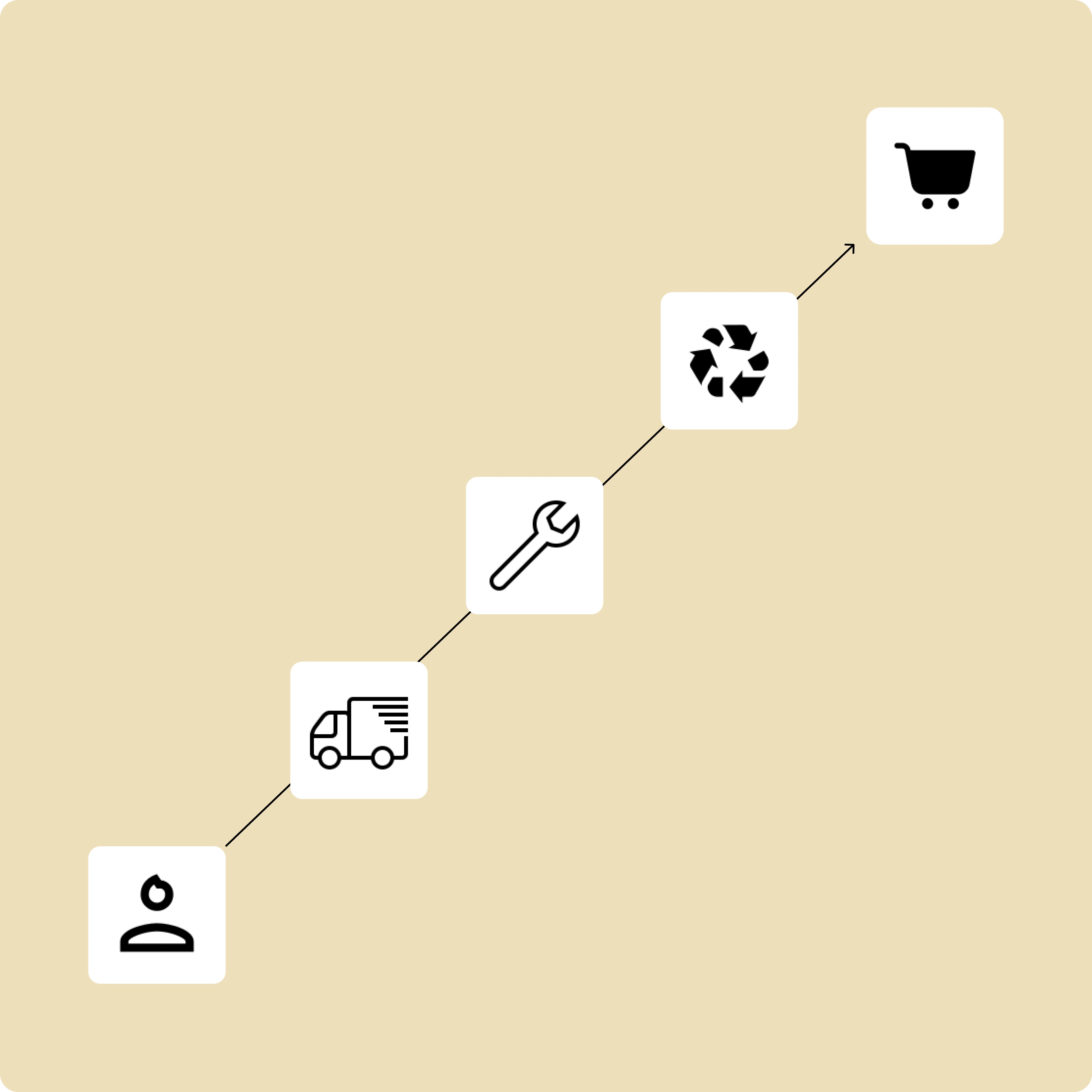
While traditional logistics focuses on getting products to customers, reverse logistics is the process of getting a product from customer back to the seller or manufacturer.
Think of returns, repairs, recycling, or product recalls. All of these fall under reverse logistics. And in the world of ecommerce, where return rates hover around 17%, having an efficient reverse logistics process is essential.
In this guide, we’ll dive into what reverse logistics is, how it works, and how businesses can optimize their reverse supply chain using the best tools and strategies.
What is Reverse Logistics?
As mentioned above, reverse logistics refers to the process of moving goods from the customer back to the seller or manufacturer. It encompasses returns, repairs, recycling, refurbishing, and disposal.
Basically it is the process of returning a product and how you create a smooth process for your customer and yourself. Remember returning products are crucial for customers: 79% of consumers check return policies before buying.
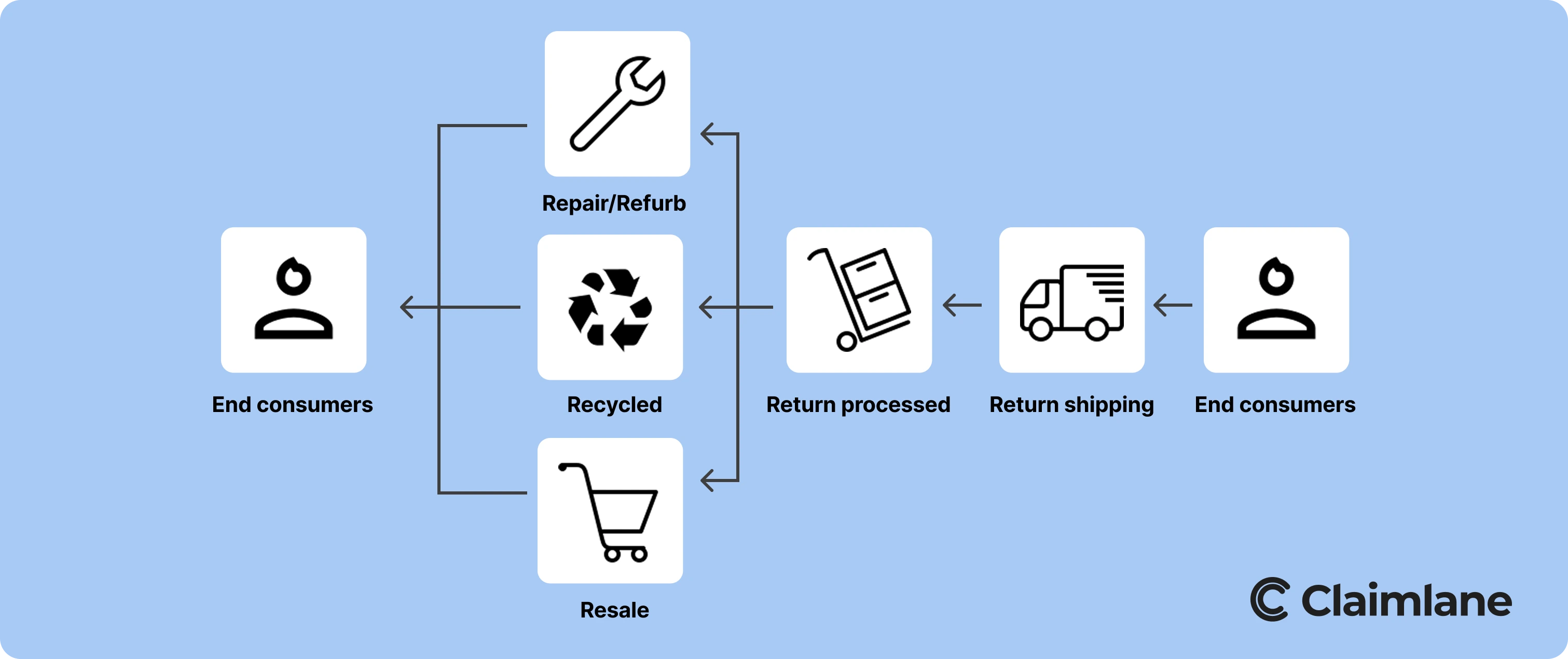
Examples of Reverse Logistics:
- A customer returns a product bought online.
- A defective item is sent back for repair under warranty.
- A company recalls a product due to a safety issue.
- Old electronics are recycled through a take-back program.
While forward logistics focuses on delivering products, reverse logistics manages what happens when things come back - and most importantly how businesses can recover value from them.
The Reverse Logistics Process
A smooth reverse logistics process ensures that returns are handled efficiently and cost-effectively.
Typical Steps in Reverse Logistics:
- Return Initiation – The customer requests a return or warranty claim.
- Return Authorization – The business issues an RMA (Return Merchandise Authorization) and provides return instructions.
- Return Shipping – The product is shipped back to the warehouse or repair center.
- Inspection and Sorting – Items are inspected and sorted for restocking, refurbishing, recycling, or disposal.
- Resolution – Refunds, replacements, or repairs are processed.
- Inventory Management – Restockable products are added back to inventory, while others are recycled or disposed of.
With the right reverse logistics process, businesses can very easily reduce costs, and improve customer satisfaction.
How do you optimize the reverse logistics process?
There are many ways optimize how you handle product returns, such as training your customer support team or updating your return policy.
But if you're looking for ways to completely change how you handle product returns, we suggest using a Warranty Management Software or Returns Management System.
This way you not only make it easier to collect returns from your customers, but you get a complete overview on all
The 5 R’s of Reverse Logistics
To optimize reverse logistics, businesses often follow the 5 R’s of reverse logistics. This is a framework for managing returns sustainably and efficiently:
- Returns – Handling product returns from customers quickly and accurately.
- Reselling – Refurbishing and reselling returned goods to recover value.
- Repairs – Fixing defective products and returning them to the customer.
- Recycling – Properly disposing of products that can’t be reused or resold.
- Repackaging – Repackaging returned products for resale when possible.
Reverse Logistics for retailers
In reverse logistics ecommerce, product returns are a common issue. Customers expect simple return policies, but handling those returns can be a logistical nightmare for some businesses.
Challenges in Reverse Logistics retail:
- Higher return rates compared to brick-and-mortar stores.
- Complex international returns and cross-border logistics.
- Increased risk of return fraud.
- Difficulty in reselling returned or opened products.
- Bulky products are not easy to handle and there can be a lot of costs involved.
Any retailer tackling their reverse logistics has two areas they should focus on: Customer experience and Internal operations.
Benefits of a Reverse Logistics management software
Managing returns manually is time-consuming and error-prone. That’s where reverse logistics management software comes in.
A manual returns process usually involves:
- Email communication with customer: A lot of back-and-forth communication to get the right information.
- Spreadsheets with manual data input.
- For ecommerce: manually reaching out to suppliers for credit notes.

Key Benefits of Reverse Logistics Software:
- Automates return authorizations (RMAs) and shipping label creation.
- A return portal removing unnecessary communication.
- Provides analytics to optimize the reverse supply chain.
- Streamlines communication between customers, warehouses, and suppliers.
The best reverse logistics software helps businesses reduce return costs, speed up processing, and improve customer satisfaction.
Different ways to solve reverse logistics issues
Many businesses face challenges in reverse logistics, but there are several approaches to solving them.
Manually handling product returns
Many companies handle their product returns manually. This is usually done with a combination of email and spreadsheet to manage their returns and warranty claims.
- Pros: Low initial cost, simple setup.
- Cons: Time-consuming, error-prone, hard to scale, lacks real-time tracking.
- Example: Managing returns through emails, spreadsheets, and manual processes.
Returns Management System
- Pros: Automates returns, improves tracking, streamlines refunds and exchanges.
- Cons: Most focus only on returns - not repairs or warranty claims.
- Example: Software that manages ecommerce returns, exchanges, and restocking.
Warranty Management System
- Pros: Handles product returns, repairs, and warranty claims.
- Cons: May require integration with other systems for full reverse logistics management.
- Example: Software that tracks warranty claims, automates approvals, and manages repairs/replacements.
The most efficient solution often involves integrating a reverse logistics management software with returns and warranty management systems for end-to-end coverage, such as Claimlane.
How Claimlane works
What you should look for in a Reverse Logistics Software
Selecting the right reverse logistics solution can make or break your return process.
What to Look For:
- Automation – Streamlines returns, repairs, and recycling.
- Integration – Connects with ecommerce platforms, ERPs, and inventory systems.
- Scalability – Handles increasing return volumes as your business grows.
- Analytics – Provides insights into return trends and product defects.
- Customer Experience – Simplifies the return process for customers.
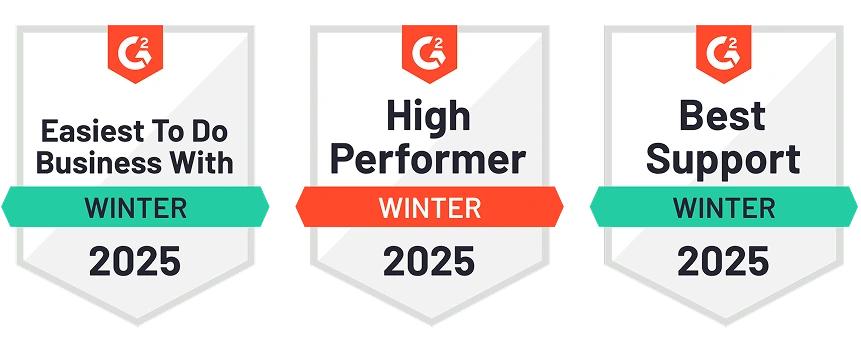
Top options in the market for the best reverse logistics software offer these features and more. While we may be biased, we believe Claimlane delivers the absolute best solution on the market.
You can also check out review sites such as G2 for either the best rated Warranty Management Software or Return Management Systems.