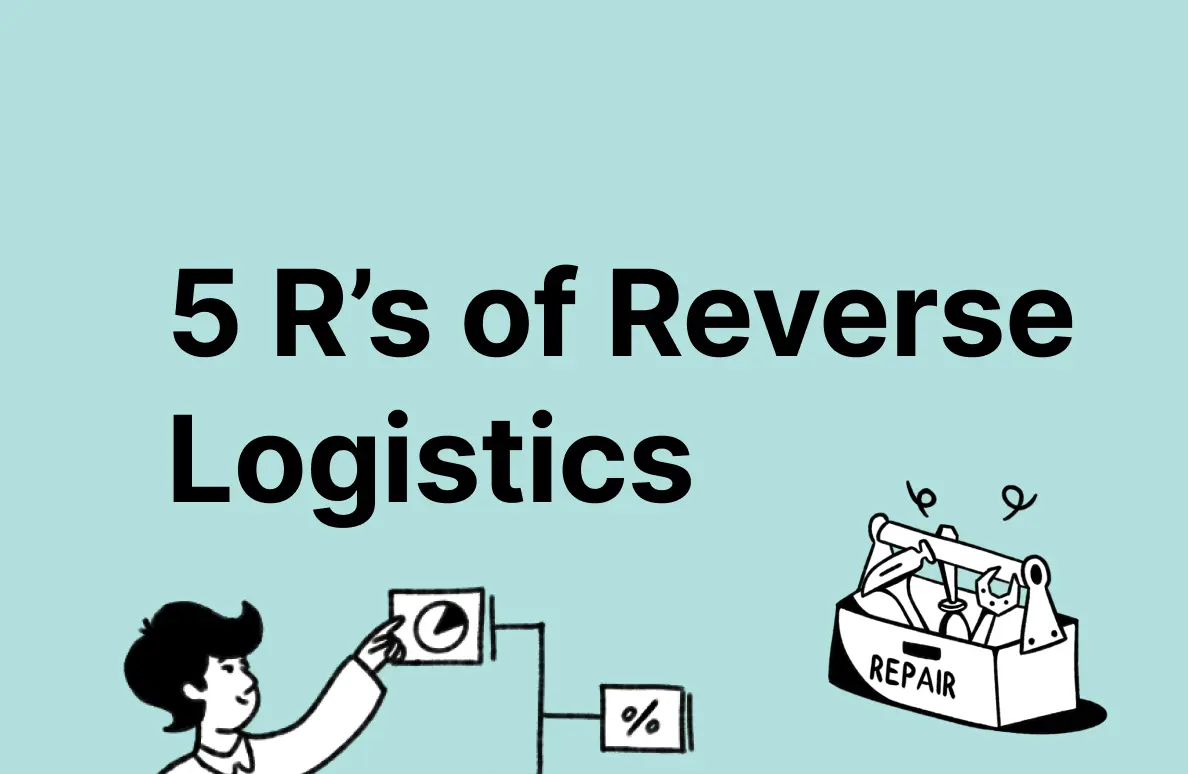
Reverse logistics involves the process of moving goods from their final destination back to the manufacturer or retailer for returns, repairs, recycling, or disposal. These 5 outcomes defines what is usually called the 5 r's of reverse logistics. Understanding and implementing these 5 R's of reverse logistics can enhance customer satisfaction, reduce costs, and promote sustainability.
What Are the 5 R's of Reverse Logistics?
The 5 R's of reverse logistics are:
- Returns
- Recalls
- Repairs
- Repackaging
- Recycling
Let's delve into each component to understand how they contribute to an effective reverse logistics strategy.
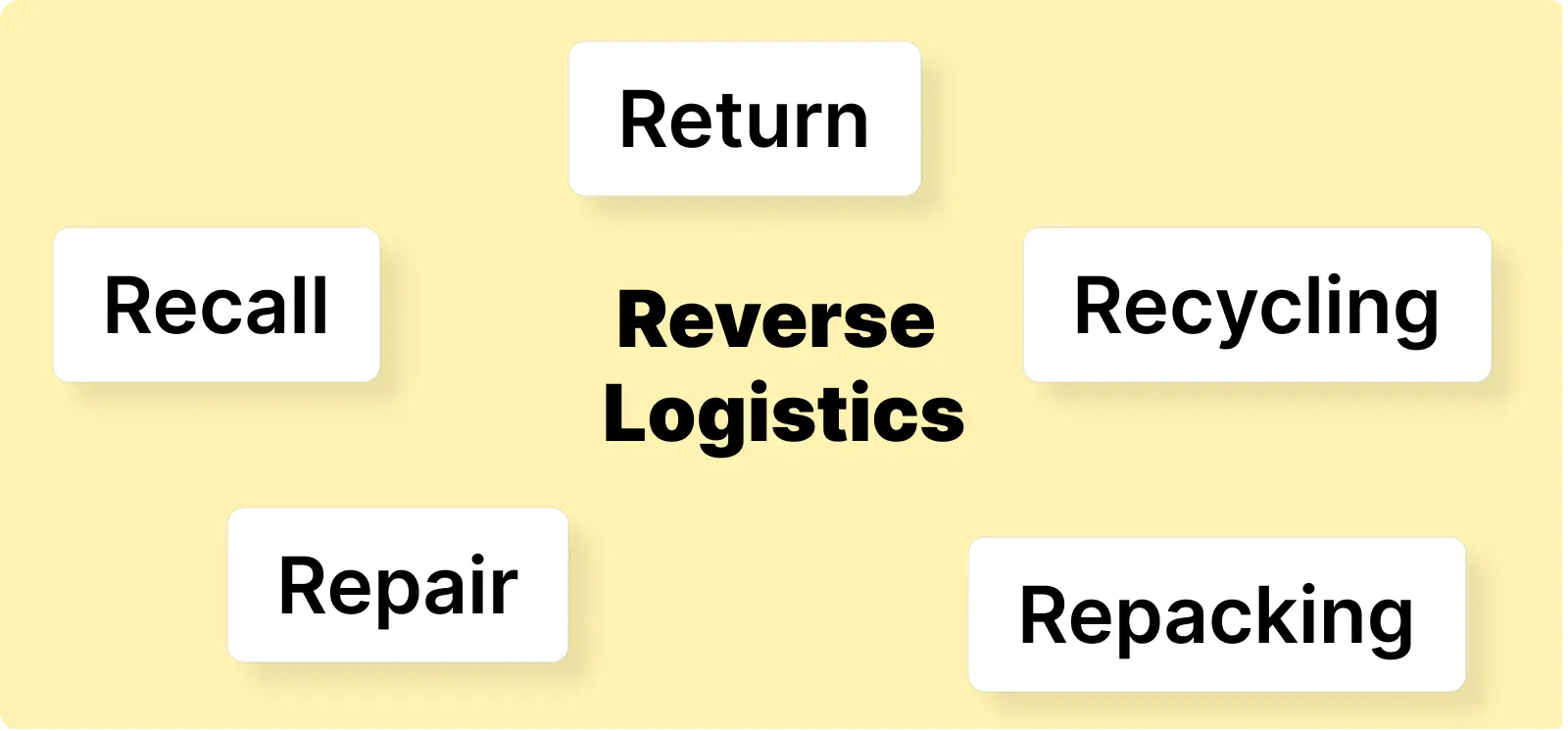
1. Returns
Returns are inevitable in any business, especially with the rise of e-commerce. The average return rate for e-commerce stores hit 18% in 2023 according Shopify. Customers may return products due to defects, damage, or simply because the item didn't meet their expectations. Efficient handling of returns is essential to maintain customer trust and loyalty.
Key Strategies:
- Clear Return Policies: Establish straightforward return policies to guide customers through the process.
- Reverse Logistics Software: Implement systems to track returns and manage inventory effectively.
- Customer Communication: Keep customers informed about the status of their returns to enhance satisfaction.
2. Recalls
Recalls occur when products are found to be defective or unsafe. Managing recalls promptly is vital to protect consumers and maintain brand reputation.
Key Strategies:
- Proactive Monitoring: Regularly assess product quality to identify potential issues early.
- Efficient Recall Processes: Develop clear procedures for recalling products swiftly and safely.
- Regulatory Compliance: Ensure all recall activities meet industry regulations and standards.
3. Repairs
Not all returned products are beyond salvage. Many items can be repaired and returned to the market, reducing waste and recapturing value.
Key Strategies:
- Assessment Protocols: Evaluate returned items to determine repair feasibility.
- Skilled Technicians: Employ qualified personnel to perform repairs efficiently.
- Quality Assurance: Test repaired products to ensure they meet original specifications.
4. Repackaging
Products returned in good condition or after repair may require repackaging before they can be resold. Proper repackaging ensures items are market-ready and appealing to customers.
Key Strategies:
- Inspection Procedures: Check products for damage before repackaging.
- Sustainable Materials: Use eco-friendly packaging to appeal to environmentally conscious consumers.
- Inventory Management: Update stock levels promptly to reflect repackaged items.
5. Recycling
When products reach the end of their lifecycle or cannot be repaired, recycling becomes the best option. Recycling helps recover valuable materials and supports environmental sustainability.
Key Strategies:
- Material Segregation: Sort products into components for efficient recycling.
- Partnerships: Collaborate with certified recycling firms to handle different materials.
- Compliance: Adhere to environmental regulations governing waste disposal and recycling.
How Claimlane Can Help Implement the 5 R's of Reverse Logistics
Managing reverse logistics efficiently requires the right tools and technology. Whether you look at a reverse logistics software solution, return management system or warranty claim solution all of them can help simplify and streamlines the 5 R’s for businesses, ensuring smooth operations and cost efficiency.
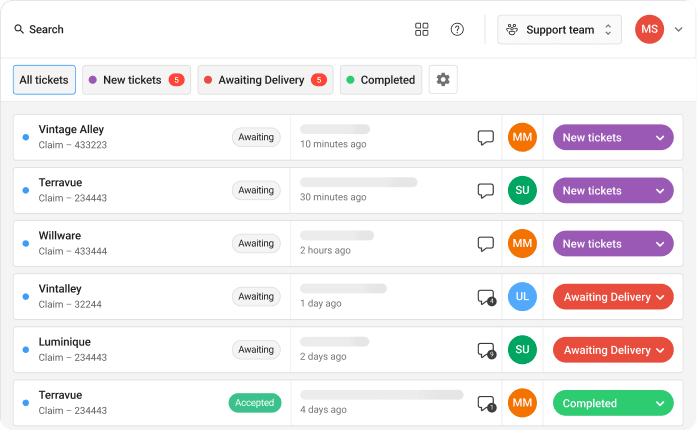
Key Benefits of Claimlane:
- Automated Returns Management: Claimlane automates the returns process, reducing manual effort and improving accuracy.
- Seamless Recall Handling: The software helps businesses create a product recall portal for defective products and coordinate recall logistics efficiently.
- Repair Workflow Optimization: Claimlane enables you to receive repair requests.
Mastering the 5 R's of reverse logistics: Returns, Recalls, Repairs, Repackaging, and Recycling, is essential for businesses aiming to optimize their supply chain operations. By implementing these strategies, companies can enhance customer satisfaction, reduce operational costs, and contribute to a more sustainable future.
Ready to transform your reverse logistics process? Contact us today to learn how Claimlane can help you implement reverse logistics in your business.