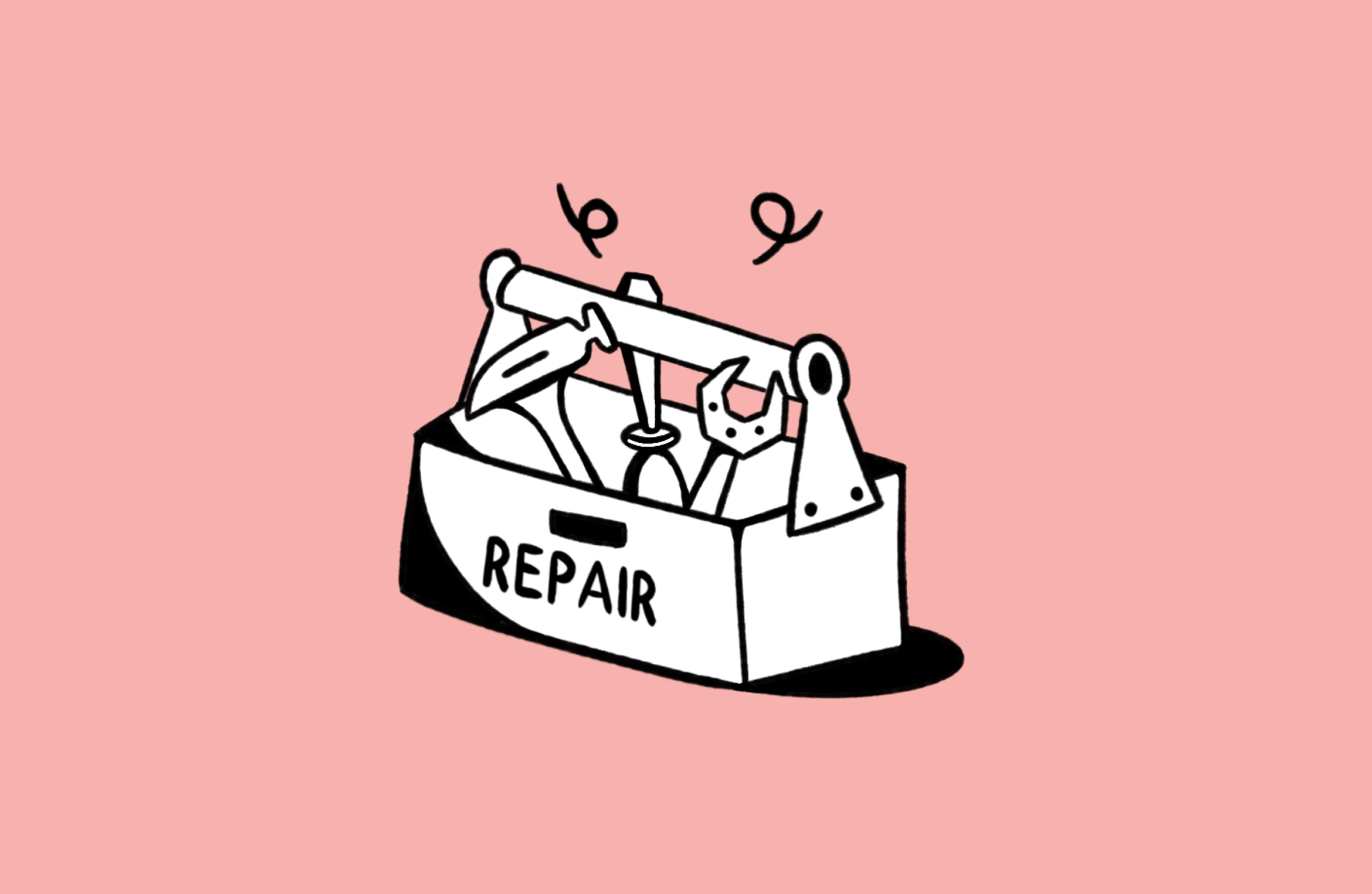
What is reverse logistics?
Reverse logistics refers to the process of managing the flow of goods or materials from the point of consumption – i.e. the customer’s delivery address – back to the point of origin or to another location, such as a retailer or brand, for returns, repairs, recycling, refurbishment, or disposal.
It is essentially the opposite of the traditional forward logistics that delivers products from retailers or brands to consumers.
Reverse logistics is a high-growth sector. Statistics show that the global reverse logistics market size in 2023 was $700.17 billion, and it is projected to reach $954.5 billion by 2029, marking a growth of 36.3%.
Reverse logistics vs traditional logistics
Reverse logistics and traditional logistics – or forward logistics – are two interconnected processes, but they focus on different directions in the supply chain and serve distinct purposes.
An efficient supply chain requires both. Forward logistics ensures products reach customers quickly and reliably, while reverse logistics ensures products are properly handled when they are no longer needed or need repair, enhancing customer satisfaction and sustainability.
Efficient integration of both systems can significantly boost operational efficiency, reduce costs, and improve customer and environmental outcomes.
The different types of reverse logistics
There are several, distinct types of reverse logistics, including the following:
- Returns Management:
This covers the handling the return of products from customers to the manufacturer, where customer returns are processed for refunds, replacements, or repairs. Resaleable items can be restocked.
- Refurbishment or remanufacturing:
This refers to the refurbishment or remanufacturing of used products to restore them to a sellable or usable condition. This might be done to extend the life of products, or to resell as certified pre-owned or refurbished items.
- Recycling and Waste Management
This is recovering materials from end-of-life products for reuse in manufacturing or ensuring their proper disposal. This might be done to reduce environmental impact and to minimize waste.
- Product Recall
This refers to retrieving products from the market due to defects, safety issues, or regulatory non-compliance, done to protect customer safety or maintain brand reputation.
- Packaging Management
This is the reclaiming and reuse of product packaging materials such as pallets, containers, or boxes, done to reduce packaging waste or lower costs associated with new packaging.
- End-of-Life (EOL) Returns
This covers managing the disposal, recycling, or refurbishment of products that have reached the end of their lifecycle. This is important for ESG purposes, providing clear evidence of the safe, responsible disposal of all materials.
- Repairs and Maintenance
Collecting faulty or damaged products from customers for repair and returning them. This is done to restore products to working condition and to enhance customer service and satisfaction levels.
- Rental and Leasing Returns
This refers to managing the return of products, such as electrical appliances or cars, after rental or lease periods. Products can then be refurbished and prepared for the next customer, ensuring efficient asset utilization.
Why is reverse logistics important?
Reverse logistics is crucial for businesses and industries for several reasons, spanning cost management, sustainability, and customer satisfaction.
One of the main areas of importance is to enhance cost efficiency. Efficiently handling returns and refurbishments reduces financial losses associated with unsold inventory or defective products, while salvaging materials through recycling, refurbishing, or reselling helps recover costs and generate additional revenue. Furthermore, products can be reintegrated into the supply chain, reducing the need for new production.
Reverse logistics is also a vital component of a company’s ESG policy. The recycling and reusing of products reduces waste sent to landfills, while recovered materials reduce dependency on raw resources, conserving energy and natural materials. There are also legislative reasons - many industries are required by law to manage waste and recycling responsibly, particularly for hazardous materials.
Enhanced levels of customer satisfaction are also important. Offering hassle-free returns and exchanges improves the customer experience, while providing repair options ensures customers feel supported, increasing loyalty and trust. Additionally, companies that actively manage returns and prioritize environmental responsibility are viewed more favourably by customers.
What are the five “Rs” of reverse logistics?
They are essential principles for optimizing value recovery, minimizing waste, and enhancing operational efficiency.
1. Returns
- Definition: The process of handling products returned by customers or end-users.
- Key Activities:
- Accepting and inspecting returned goods.
- Processing refunds, replacements, or repairs.
- Purpose:
- Improve customer satisfaction.
- Recover usable inventory.
- Example: A retailer managing online order returns and restocking resalable items.
2. Reselling
- Definition: Selling returned, refurbished, or excess products in secondary markets or directly to new customers.
- Key Activities:
- Repairing and certifying products as refurbished.
- Identifying secondary markets for overstock or returned goods.
- Purpose:
- Recapture value from unsold inventory.
- Reduce financial losses.
- Example: Electronics companies selling refurbished devices through certified outlets.
3. Repairs
- Definition: Fixing defective or damaged products to restore functionality.
- Key Activities:
- Diagnosing product issues.
- Replacing or repairing faulty components.
- Purpose:
- Extend product life.
- Reduce waste and maintain customer trust.
- Example: Smartphone manufacturers offering repair services for out-of-warranty devices.
4. Recycling
- Definition: Recovering materials from used or end-of-life products for reuse in manufacturing or proper disposal.
- Key Activities:
- Sorting and dismantling products.
- Extracting valuable raw materials like metals or plastics.
- Purpose:
- Minimize environmental impact.
- Support sustainability initiatives.
- Example: Recycling e-waste such as old laptops or batteries to reclaim metals like lithium and cobalt.
5. Replacements
- Definition: Providing customers with new or equivalent products in exchange for defective, damaged, or unsatisfactory ones.
- Key Activities:
- Ensuring efficient inventory management for replacement stock.
- Handling exchanges quickly to maintain customer satisfaction.
- Purpose:
- Build customer loyalty.
- Uphold brand reputation by ensuring product quality.
- Example: A clothing retailer offering size exchanges or replacements for defective garments.
The benefits of reverse logistics
Reverse logistics offers numerous benefits to businesses, customers, and the environment by streamlining processes for handling returns, recycling, and waste management:
- Cost Savings
- Value Recovery: Refurbishing, reselling, or recycling returned goods can recapture value that would otherwise be lost.
- Reduced Disposal Costs: Recycling and reusing components lower the costs associated with waste disposal.
- Improved Inventory Management: Returned goods can be reintroduced into the supply chain, reducing the need for new production.
- Increased Customer Satisfaction
- Seamless Returns Process: Providing efficient and convenient return options enhances customer trust and loyalty.
- Improved Brand Perception: Customers appreciate businesses that offer hassle-free returns, repairs, and replacements.
- Extended Product Support: Repair and refurbishment services demonstrate a commitment to product longevity and customer care.
- Environmental Sustainability
- Waste Reduction: Recycling materials from returned products minimizes landfill waste.
- Resource Conservation: Recovering and reusing components reduces the demand for raw materials.
- Support for Circular Economy: Promoting product life extension and recycling aligns with sustainability initiatives and regulations.
- Compliance with Regulations
- Meeting Environmental Standards: Proper disposal and recycling of hazardous materials ensure compliance with laws.
- Avoiding Penalties: Efficient reverse logistics reduces the risk of fines and legal issues related to waste management.
- Competitive Advantage
- Sustainability Leadership: Businesses that excel in reverse logistics are often viewed as industry leaders in sustainability.
- Differentiation: Offering better return policies, recycling programs, or refurbished products sets a company apart from competitors.
- Improved Operational Efficiency
- Streamlined Processes: A well-organized reverse logistics system reduces delays in managing returns and recycling.
- Insights from Returns: Data from returned products can highlight defects or areas for improvement, enhancing forward logistics operations.
- Support for Revenue Generation
- Secondary Market Opportunities: Selling refurbished or excess inventory opens new revenue streams.
- Customer Retention: Happy customers are more likely to make repeat purchases.
- Enhanced Supply Chain Resilience
- Resource Optimization: Recovered components or products act as a buffer during supply chain disruptions.
- Inventory Balancing: Returned products can help meet demand without additional manufacturing.
The reverse logistics process
The reverse logistics process involves managing the movement of goods from their destination back to the manufacturer, supplier, or designated facility. This process typically includes several stages aimed at efficiently handling returns, refurbishments, recycling, or disposal.
- Description: Initiated when a customer, retailer, or distributor sends a product back due to reasons such as defects, dissatisfaction, or end-of-life.
- Key Activities:
- Identifying the reason for the return.
- Authorizing the return through a Return Merchandise Authorization (RMA).
- Collecting and shipping the product to a designated facility.
- Example: A customer returning a defective smartphone to a retailer.
2. Inspection and Sorting
- Description: Products are inspected upon arrival to assess their condition and determine the appropriate next steps.
- Key Activities:
- Visual and functional inspection.
- Categorization into groups (e.g., repairable, resalable, recyclable, or disposable).
- Example: Sorting returned electronics into functional items for resale and non-functional ones for recycling.
3. Processing
- Description: Based on the inspection, products undergo necessary processing.
- Key Activities:
- Repairing or refurbishing products for resale.
- Disassembling items for recycling materials.
- Cleaning and repackaging products if suitable for resale.
- Example: Refurbishing returned laptops for resale as certified pre-owned devices.
4. Restocking or Reselling
- Description: Products that are fit for use are reintroduced into the supply chain.
- Key Activities:
- Restocking returned items in inventory.
- Selling refurbished products in secondary markets or as "open-box" items.
- Example: A retailer reselling returned clothing that is in like-new condition.
5. Recycling and Waste Management
- Description: Products that cannot be reused or repaired are sent for recycling or safe disposal.
- Key Activities:
- Extracting valuable materials like metals or plastics.
- Ensuring proper disposal of hazardous materials.
- Example: Recycling old batteries to recover lithium and cobalt.
6. Data Collection and Analysis
- Description: Gathering insights from the returns process to improve forward logistics and product design.
- Key Activities:
- Tracking return trends and reasons.
- Using data to refine manufacturing and quality control processes.
- Example: Analyzing frequent returns of a product due to a design flaw and addressing the issue in future manufacturing.
7. Disposal (If Necessary)
- Description: Products that cannot be repaired, resold, or recycled are responsibly disposed of.
- Key Activities:
- Complying with environmental regulations.
- Minimizing landfill impact.
- Example: Safe disposal of medical equipment that cannot be reused or recycled.
The challenges in reverse logistics
Reverse logistics, while beneficial in the multiple ways that we have outlined, poses significant challenges due to the complexity of managing the backward flow of goods. Here are the primary challenges:
1. Unpredictable Return Volumes
- Description: Difficulty in forecasting the number and timing of returns leads to inconsistent workflows.
- Impact:
- Overstaffing or understaffing in return processing centers.
- Inventory management issues.
- Example: A surge in returns after major shopping events like Black Friday.
2. High Costs
- Description: Managing reverse logistics can be expensive due to labor, transportation, and processing costs.
- Impact:
- Reduced profit margins.
- Increased operational burden.
- Example: Shipping costs for returns often exceed those for initial delivery.
3.Complex Processes
- Description: Handling varied return reasons (e.g., defective, unwanted, end-of-life) adds complexity.
- Impact:
- Slower processing times.
- Increased error rates.
- Example: Sorting defective products from resalable items requires detailed inspection.
4. Poor Visibility and Tracking
- Description: Limited real-time tracking and visibility of returned goods in the supply chain.
- Impact:
- Delays in identifying return statuses.
- Inefficiencies in restocking or recycling.
- Example: Losing track of returned items due to inadequate tracking systems.
5. Lack of Standardization
- Description: Inconsistent policies and procedures across regions or facilities.
- Impact:
- Mismanagement of returns.
- Increased confusion for customers and staff.
- Example: Different return policies for online and in-store purchases.
6. Handling Diverse Product Types
- Description: Processing a wide range of products, each requiring different handling, repair, or recycling procedures.
- Impact:
- Increased operational complexity.
- Need for specialized equipment or expertise.
- Example: Processing returned electronics versus returned clothing.
How to improve reverse logistics
Improving reverse logistics involves optimizing processes, leveraging technology, and adopting sustainable practices to enhance efficiency, reduce costs, and satisfy customers. Here are some of the strategies to improve reverse logistics:
1. Streamline the Returns Process
- Simplify Returns for Customers:
- Offer clear instructions and user-friendly return portals.
- Provide prepaid return labels or easy drop-off points.
- Automate Returns Authorization:
- Use Return Merchandise Authorization (RMA) systems to quickly approve and track returns.
2. Invest in Technology
- Implement Tracking Systems:
- Use barcodes, RFID, or IoT-enabled devices to monitor returns in real-time.
- Leverage Data Analytics:
- Analyze return trends to predict volumes and identify root causes of product issues.
- Adopt Reverse Logistics Management Software:
- Integrate specialized software for handling returns, repairs, and recycling efficiently.
3. Establish Centralized Returns Centres
- Centralize Processing:
- Consolidate returns at specific locations to reduce transportation costs and streamline sorting.
- Optimize Facility Layouts:
- Design facilities for efficient inspection, repair, refurbishment, and recycling workflows.
4. Implement Standardized Policies
- Uniform Return Policies:
- Standardize return policies across all channels (e.g., online and in-store) to minimize confusion.
- Clear Guidelines for Handling:
- Define processes for inspecting, repairing, reselling, or recycling returned products.
5. Enhance Customer Communication
- Provide Real-Time Updates:
- Notify customers of the status of their returns, repairs, or replacements.
- Educate Customers:
- Share guidelines on proper packaging for returns to reduce damage during transit.
6. Focus on Value Recovery
- Refurbish and Resell:
- Establish programs to repair and resell returned goods as refurbished or open-box items.
- Identify Secondary Markets:
- Explore alternative markets for selling surplus or returned inventory.
- Maximize Recycling Efforts:
- Partner with recyclers to extract value from end-of-life products.
Reverse logistics examples
It is crucial to emphasise that a solid reverse logistics platform, such as Claimlane’s, can offer a fully bespoke reverse logistics programme on behalf of clients across a vast range of sectors, be in furniture, homeware, DIY, the baby and nursery sector or fashion and retail.
Indeed, Claimlane currently operates multiple reverse logistics packages for its clients across the globe.
Looking at what exists for high-profile names, there are endless examples, including one of the globe’s most instantly recognisable names, Amazon, which efficiently manages returns and resells or recycles items, reducing waste and costs. Similarly, Apple operates a robust refurbishment and recycling program for old devices, recovering valuable materials like rare earth metals.
In the clothing sector, Patagonia ecourages customers to return used clothing for recycling or resale, promoting sustainability and extending product life.
As we have seen, operating an intuitive reverse logistics programme can provide multiple benefits to businesses operating across numerous sectors.
If you would like to know more about how Claimlane can help, feel free to reach out and hear how we can help with your reverse logistics.